PLCs and Electrical Controls
At DevLinks, we integrate advanced PLC and Electrical Control Systems into every automation and robotics work cell we create, ensuring seamless operation, safety, and ease of use. Our systems are designed to enhance productivity and reduce downtime, giving you a powerful and reliable foundation for your manufacturing operations.
Whether you’re running a single robot or an entire automated production line, our PLC-based control systems offer real-time communication, user-friendly interfaces, and detailed system diagnostics.
Key Features of Our PLC & Electrical Control Systems
Operator Interfaces
We use Maple Systems Operator Interface Terminals (HMI) in 7” or 15” displays, enabling operators to easily input commands, monitor system status, and access critical information.
Start-Up Sequences & Status Updates
The HMI shows start-up sequences and real-time status updates, allowing operators to quickly identify system states and errors, minimizing downtime.es
- Error logs
Error Monitoring & Diagnostic
With error displays available on the HMI, operators are notified of the exact cause of any system issues. This immediate feedback allows quick action and minimizes the impact of line stoppages.
Data Collection
Our standard HMI programming includes basic data collection such as:
- Uptime/Downtime tracking
- Total parts completed
This real-time data helps you monitor performance and make informed decisions to optimize your processes.
Electrical Components and Integration
We use Allen Bradley components to ensure the highest standards in system performance and reliability. Here’s what you can expect in a typical DevLinks automation and robotics work cell:
- Allen Bradley Compact Logix E Series PLC
- Allen Bradley I/O components for seamless communication
- NEMA 12 Enclosures for PLC and I/O chassis, ensuring reliable protection and safety
- Safety and control relays integrated with the system ensure safety compliance
- All electrical systems are constructed in accordance with NEC – NFPA79 and housed in NEMA12-rated enclosures
- External hardware (sensors, etc.) rated NEMA 12 or better (IP67 for sensors)
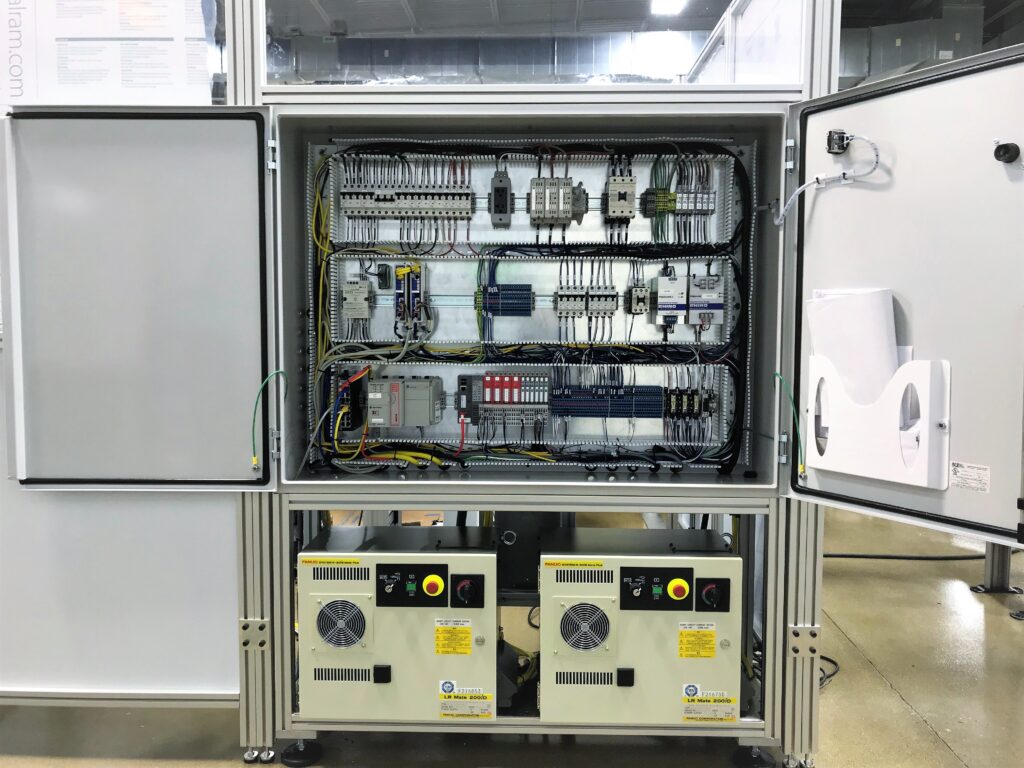
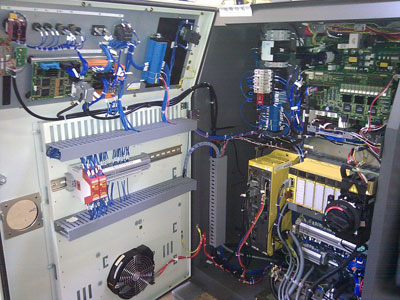
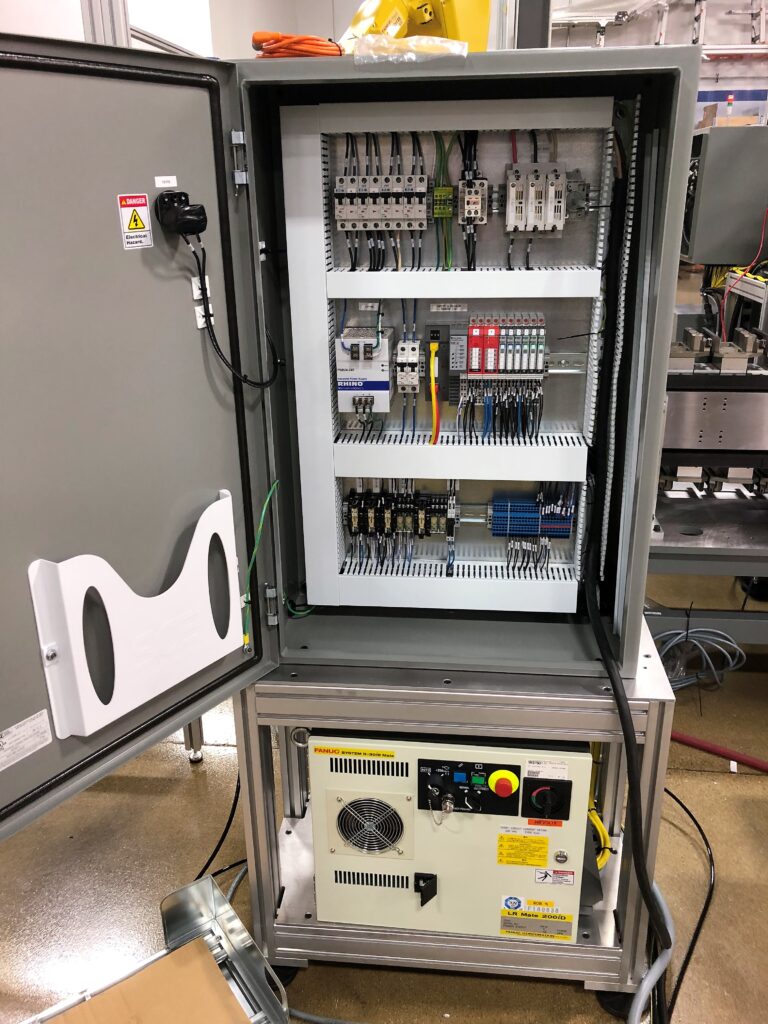
Need a customized PLC system for your work cell? Get in touch with our experts!
Our systems also feature Ethernet and discrete I/O interfacing, enabling direct communication with Fanuc Robots, ensuring smooth integration across the entire work cell.